QC Planning and Scheduling Software to Optimize Pharmaceutical Operations
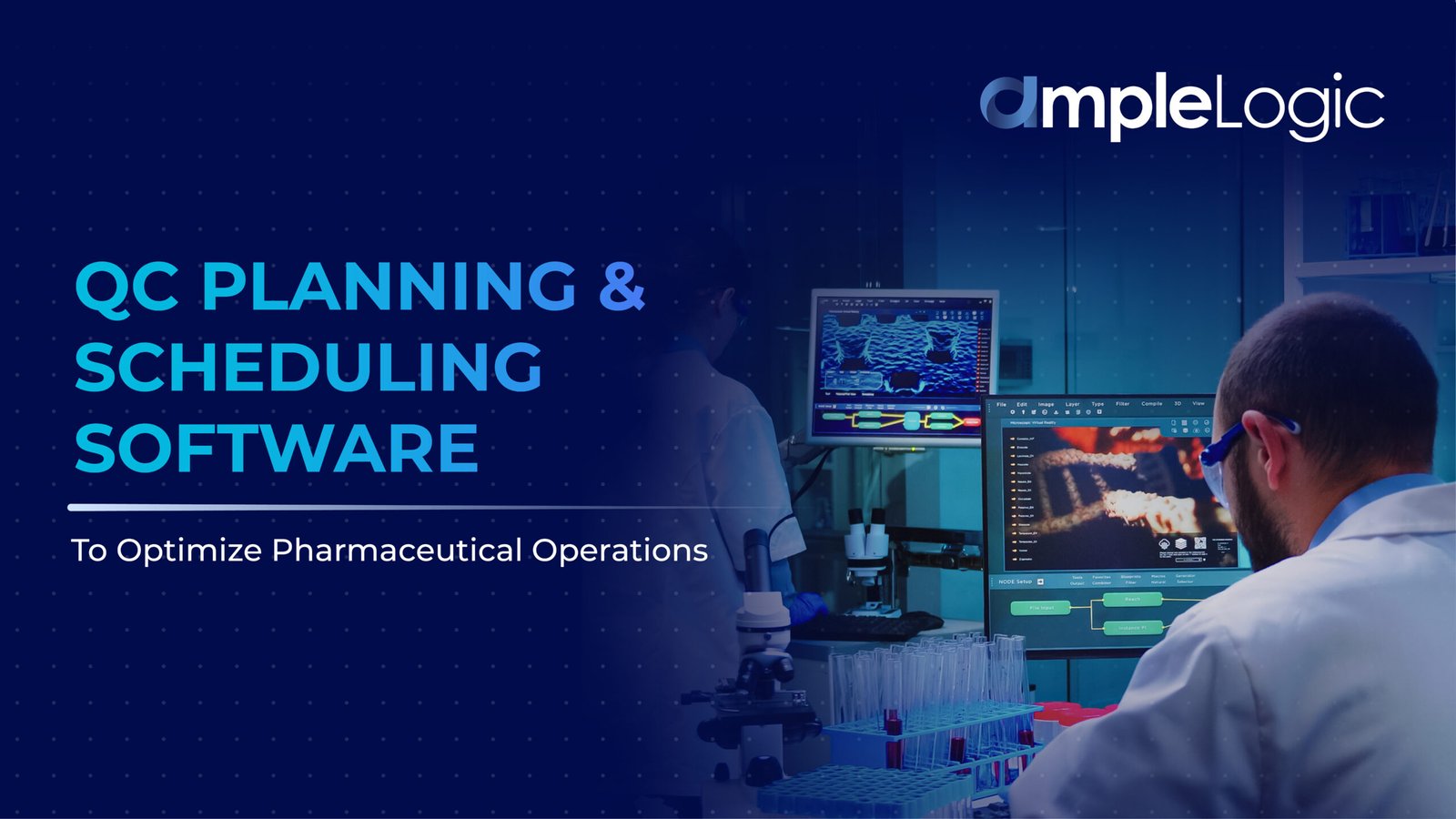
Pharmaceutical quality control (QC) is the backbone of ensuring product safety, efficacy, and compliance. However, managing QC laboratory processes in the pharmaceutical industry presents a range of challenges that can disrupt operations and jeopardize product quality. From scheduling conflicts and resource allocation inefficiencies to the risk of non-compliance, these obstacles can have a significant impact on timelines, costs, and overall efficiency. In this article, we will explore the key challenges faced in QC planning and scheduling and how addressing them can lead to improved operational outcomes and regulatory compliance.
Challenges in Pharma Quality Control Planning and Scheduling
Pharmaceutical quality control (QC) is crucial to ensuring the safety, efficacy, and compliance of products. However, managing QC laboratory processes in a pharmaceutical environment comes with several challenges that can hinder operational efficiency and regulatory compliance. These challenges can impact timelines, resource utilization, and product quality. Here are some of the key challenges faced in pharma QC planning and scheduling:
- Scheduling Conflicts
In pharmaceutical manufacturing, equipment and personnel are often shared across multiple departments. Without an automated system to track availability, scheduling conflicts can arise, causing delays, downtime, and inefficiencies. This is particularly problematic when QC laboratory activities, such as batch testing or equipment calibration, are not properly aligned with production schedules.
- Resource Allocation Inefficiencies
Ineffective resource allocation is a common challenge in QC planning. Analysts, lab equipment, and testing resources need to be assigned efficiently to avoid overburdening certain resources or underutilizing others. Poor resource allocation can lead to bottlenecks, delays, and increased operational costs.
- Human Error and Manual Workload
Manual data entry and tracking are prone to errors, which can compromise the accuracy and consistency of QC laboratory processes. Manual scheduling, test recording, and reporting increase the likelihood of mistakes, leading to delayed results, inaccurate data, and potential compliance issues. Additionally, human error can affect decision-making, further slowing down operations.
- Regulatory Compliance Risks
Pharmaceutical companies must comply with stringent regulatory standards such as Good Manufacturing Practices (GMP) and Good Laboratory Practices (GLP). Ensuring compliance manually can be time-consuming and error-prone. Inconsistent documentation, lack of traceability, and improper tracking of tests and batches increase the risk of non-compliance, which can result in costly fines, delays, and reputational damage.
- Test Turnaround Time (TAT) Delays
Meeting production deadlines and ensuring timely release of batches is critical in pharma operations. Delays in test results, inadequate scheduling, and lack of coordination between departments can lead to prolonged Test Turnaround Time (TAT). This negatively impacts production timelines, inventory management, and supply chain efficiency.
- Lack of Real-Time Monitoring
In traditional QC planning systems, there is often limited visibility into the real-time status of QC laboratory activities. Without real-time updates, managers cannot quickly identify and address issues, such as delayed tests, equipment malfunctions, or staffing shortages. This lack of monitoring can lead to prolonged downtimes and missed opportunities for process optimization.
- Inconsistent SOP Adherence
Adherence to Standard Operating Procedures (SOPs) is critical in maintaining quality and compliance. However, ensuring that all QC activities are performed according to SOPs across different shifts and teams can be challenging when tracking is done manually. Non-compliance with SOPs can lead to quality deviations, which may affect the safety and efficacy of pharmaceutical products.
- Scalability Issues
As pharmaceutical companies grow, the complexity of managing QC tasks also increases. Scaling up QC operations without compromising quality and efficiency is a significant challenge. Manual processes and legacy systems may struggle to handle the increased volume of tests, data, and resources, leading to inefficiencies and errors.
Addressing these challenges requires a robust and automated QC planning and scheduling system to streamline workflows, optimize resource utilization, and ensure compliance.
The Need for QC Planning and Scheduling Software
Laboratory quality control software addresses critical challenges in pharmaceutical labs by automating key tasks, optimizing laboratory resource scheduling, and ensuring regulatory compliance. This software enhances operational efficiency, reduces turnaround times, and improves accuracy, ultimately helping companies streamline workflows and bring products to market faster. It automates test scheduling based on analyst availability and expertise, ensures laboratory resource scheduling and utilization, and provides real-time visibility into lab performance. The software ensures compliance with standards like FDA 21 CFR Part 11 and MHRA, while eliminating paper-based processes through electronic scheduling. Additional features include customizable reports, lab capacity planning, task grouping, real-time resource tracking, email notifications, and alerts. It also supports Turnaround Time (TAT) compliance, equipment utilization tracking, and integrates biometric attendance, enhancing overall lab efficiency.
AmpleLogic QC Planning and Scheduling Software
AmpleLogic’s QC Planning and Scheduling Software transforms quality control operations across the Life Sciences industry, including Pharma, Biotech, and CROs. By automating key tasks like sample scheduling, laboratory resource scheduling and allocation, and regulatory compliance tracking, it significantly enhances lab efficiency and reduces manual intervention. With features like real-time visibility, qualification-based test scheduling, and automated sample campaigning, AmpleLogic optimizes laboratory resource scheduling and utilization and accelerates batch release, ensuring timely and accurate testing. Designed to meet FDA standards, the software streamlines workflows, reduces operational delays, and improves turnaround times (TAT), helping organizations meet stringent regulatory requirements while boosting productivity. Whether you need to manage high volumes of samples or handle urgent retests, AmpleLogic offers the flexibility, scalability, and reliability required to optimize QC lab operations.
Delve into the Features!
- Paperless Lab Scheduling: Create shift-based plans and automate test scheduling based on analyst availability, qualifications, and expertise.
- Short and Long-Term Scheduling: Support single-click test planning for both short-term and long-term scheduling needs.
- Automated Sample Campaigning: Prioritize and group samples efficiently for streamlined analysis.
- Real-Time Visibility: Gain insights into lab performance, resource utilization, and equipment availability with customizable reports and infographic dashboards.
- Lab Capacity Planning: Optimize laboratory resource scheduling and allocation by tracking tasks, time spent, and estimated durations.
- Task Grouping: Group samples based on predefined criteria to reduce overall test cycle times.
- Regulatory Compliance: Ensure compliance with FDA 21 CFR Part 11, MHRA, and EU Annex 11 standards with secure audit trails and electronic signatures.
- TAT Compliance: Track and ensure adherence to Turnaround Time (TAT) as a key performance indicator.
- OOS Report Generation: Generate Out of Specification (OOS) reports using user-defined templates.
- Equipment Blocking: Block equipment during OOS or Root Cause Analysis for effective resource management.
- Email Notifications: Automate communication for scheduled tasks, escalations, and updates.
- Task Scheduling: Efficiently manage workflows with a task scheduler for streamlined operations.
- Real-Time Resource Tracking: Track the availability of QC analysts and instruments in real-time for optimal resource allocation.
- Equipment Utilization Reports: Monitor equipment usage, downtime, and allocation to streamline production planning.
- Infographic Dashboards: Auto-generate weekly/monthly reports and KPI-based dashboards for performance monitoring.
- Biometric Integration (Upcoming): Enhance attendance tracking accuracy with biometric systems.
Pharmaceutical quality control is essential for ensuring product safety, efficacy, and regulatory compliance, but it comes with significant operational challenges. Issues like scheduling conflicts, inefficient resource allocation, manual errors, and delayed test turnaround times can impact timelines, costs, and overall productivity.
Implementing a robust laboratory quality control software is the key to overcoming these challenges. By automating test scheduling, optimizing resource utilization, and providing real-time visibility into lab performance, this software streamlines workflows and ensures compliance with global regulatory standards.
AmpleLogic’s laboratory quality control software empowers pharmaceutical, biotech, and CRO organizations to manage QC processes efficiently. With features like automated scheduling, lab capacity planning, and regulatory compliance tracking, it reduces manual intervention, improves decision-making, and accelerates batch release. Designed to handle growing QC complexities, AmpleLogic’s solution enhances operational efficiency, enabling organizations to meet stringent deadlines while maintaining high-quality standards.