
Calibration Management Software in the pharmaceutical sector is used with great importance in accuracy and compliance related to measurement instruments used in production and quality checks. It streamlines the tracking, scheduling, and execution of calibration activities, maintaining instruments within specified endurance. This calibration management software helps in regulatory standards such as Good Manufacturing Practices (GMP) and provides comprehensive documentation for audits. Its integration with inventory management systems optimizes resource allocation and minimizes downtime, ultimately contributing to the consistent quality of pharmaceutical products.
The Need for Advanced Preventive and Calibration Management
Calibration management is an essential function in several industrial sectors among them being manufacturing, health, and pharmaceutical industries. These processes ensure that equipment and instruments function correctly, reduce downtime, and prevent costly replacements. The traditional methods of managing maintenance and calibration often involve manual tracking, paper-based records, and reactive approaches. These methods are not only time-consuming but also prone to errors.
This integration of advanced technologies such as the Internet of Things (IoT), artificial intelligence (AI), and cloud computing, into preventive and calibration management software has a new era of efficiency and precision. These next-gen solutions offer benefits, from automated scheduling and real-time monitoring to predictive analytics compliance management
Key Features of Next-Gen Calibration Management Software
Automated Scheduling and Reminders
It streamlines the planning and execution of Calibration activities by automatically scheduling tasks based on predefined interval events. This feature enables timely maintenance of instruments, reduces the risk of missed calibrations, and enhances compliance with regulatory requirements. It sends reminders to relevant personnel, minimizing the possibility of oversight and optimizing workflow efficiency.
Real-Time Monitoring and Data Collection
IoT validates sensors and devices that continuously monitor equipment performance and environmental conditions. Real-time data enables organizations to function more effectively by providing accurate and up-to-date information that reduces the amount of time required for equipment maintenance and replacements.
Predictive Analytics
Artificial Intelligence and Machine learning are also utilized to analyse previous data to identify future faults in equipment maintenance requirements. With this approach it helps organizations to be prepared for certain challenges, when it comes to maintenance they do not have to wait for breakdowns and then make expensive repairs. Predictive analytics also optimize for calibration schedules, ensuring instruments remain within their specified accuracy ranges.
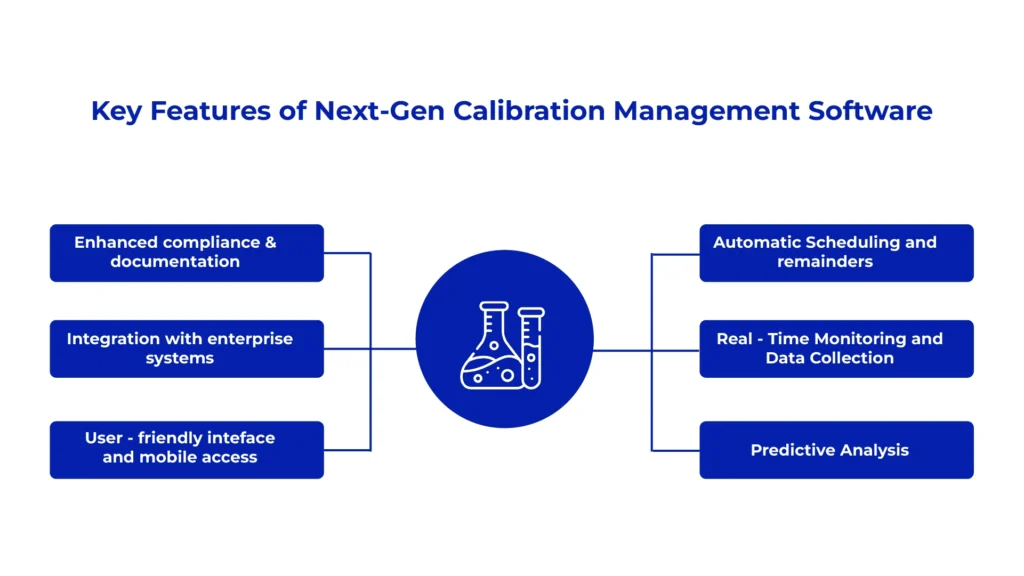
Â
Enhanced Compliance and Documentation
Compliance with industry regulations and standards is a critical aspect of maintenance and calibration. Next-gen calibration management software provides comprehensive documentation and reporting capabilities, ensuring that all maintenance and calibration activities are thoroughly documented and easily accessible. This not only simplifies audits but also ensures adherence to regulatory requirements.
Integration with Enterprise Systems & Measurement devices
Advanced calibration management software works seamlessly with other enterprise systems like Enterprise Resource Planning (ERP) and Computerized Maintenance Management Systems (CMMS). This integration creates an approach to asset management, simplifying workflows and enhancing data accuracy throughout the organization. Moreover, integrating with measurement devices and instruments allows for direct data transfer and automated collection during calibration activities. This integration not only improves data accuracy but also reduces manual errors.
User-Friendly Interfaces and Mobile Access
The latest calibration management software solutions come with easy-to-use interfaces and mobile access, allowing technicians and managers to get information, schedule tasks, and enter data on the go. This mobility boosts productivity and ensures that maintenance and calibration activities are done efficiently, even in remote or challenging locations.
Benefits of Implementing Next-Gen Preventive and Calibration Management
Improved Equipment Reliability and Performance
By ensuring timely maintenance and accurate calibration, organizations can maintain the reliability and performance of their equipment. This leads to consistent product quality, reduced scrap rates, and enhanced customer satisfaction.
Cost Savings
Scheduled maintenance and calibration help to decrease the future of equipment malfunctions, which leads to a decrease in repair costs and time for production. Further, optimized calibration schedules help to avoid over-calibration that would in turn be costly in terms of time and other necessary resources.
Enhanced Compliance and Risk Management
With comprehensive documentation and automated compliance features, organizations can easily meet regulatory requirements and pass audits. This reduces the risk of non-compliance penalties and enhances overall risk management.
Increased Operational Efficiency
Automation, real-time monitoring, and predictive analytics streamline maintenance and calibration processes, freeing up valuable resources and reducing administrative burdens. This increased efficiency allows organizations to focus on core business activities and strategic initiatives.
Data-Driven Decision Making
Access to real-time data and advanced analytics empowers organizations to make informed decisions regarding equipment maintenance and calibration. This data-driven approach enhances operational planning, resource allocation, and overall strategic management.
Best Industry for Preventive and Calibration Management
Calibration management software is versatile and applicable across various industries where equipment reliability, precision, and compliance are critical. Here are several industries that can significantly benefit from such software:
Pharmaceutical Industry: The pharmaceutical industry demands high precision in manufacturing and research to ensure product quality and patient safety.
Medical Device Manufacturing Industry: Medical devices and equipment must be regularly maintained and calibrated to provide accurate diagnostics and treatment.
Manufacturing Industry: In manufacturing, machinery and equipment require regular maintenance to prevent breakdowns and ensure production efficiency.
Aerospace and Defence: This industry relies on highly precise and reliable equipment for safety and operational effectiveness.
Energy Sector (Oil, Gas, and Renewable Energy): Energy production and distribution equipment must be regularly maintained and calibrated to avoid failures and ensure efficient operation.
Food and Beverage Industry: Equipment used in food production must be precisely calibrated to ensure product quality and safety.
Automotive Industry: Automotive manufacturing relies on precision machinery and tools that require regular maintenance and calibration.
Chemical and Petrochemical Industry: Equipment used in chemical processing must be maintained and calibrated to ensure safety and product quality.
Biotechnology: Biotechnology relies on precision equipment for research and production, requiring regular maintenance and calibration management software.
The Future of Calibration Management
In the coming future, calibration management software is going to emerge more powerful as technology is advancing constantly. Innovations such as AR and VR technologies provide possibilities for revolutionizing the learning and assistance aspects of maintenance and calibration work. Moreover, by getting even more intertwined with digital models of actual physical assets, then we may discover exceptional new avenues for understanding how the equipment operates and what is required for it to stay functional and optimized.
Conclusion
Cutting-edge calibration management software is making progress in ensuring the reliability and accuracy of equipment. By leveraging automation real-time data and predictive analytics companies can enhance their efficiency reduce expenses and maintain compliance. With an increasing number of sectors embracing these tools the outlook, for maintenance and calibration management software appears promising advancements, in innovation, efficiency, and precision.