
Cleaning validation in pharmaceutical industry is an essential process outlined by regulatory bodies to maintain product quality and prevent cross contamination. The pharma industry needs to take care that their products are not contaminated and are safe for human consumption and use. Pharma products can be contaminated by a variety of contaminants associated with microbes or previous products (both active pharmaceutical ingredients (API) and excipient residues) or residues of cleaning agents, airborne materials such as dust and particulate matter, lubricants, etc.
Regulatory bodies like the USFDA, EU EMA, and PDA set forth specific procedures that pharmaceutical companies must follow to clean their equipment and vessels after producing a batch. Pharmaceutical cleaning validation is a crucial aspect of Good Manufacturing Practices (GMP), aimed at preventing contamination and cross-contamination of pharmaceutical products. This process is verified through documented evidence, confirming that the approved cleaning procedures have been correctly followed to ensure drug products are not adulterated.
Pharmaceutical Cleaning Validation Software
Pharmaceutical cleaning validation process can be tedious and often lack supervision that is essentially needed. Manually conducting cleaning validation can lead to issues that can directly affect pharma product quality or may lead to breach in data integrity. To streamline the pharmaceutical cleaning validation procedure, companies can easily adopt a cleaning validation software that helps in generating accurate cleaning validation reports for regulatory bodies. This enhances operational efficiency and helps the pharma industry maintain product quality and comply with regulations.
Regulations for Cleaning Validation in Pharma
U.S. Food and Drug Administration (FDA)
The FDA’s revised guidance on Equipment Cleaning under Section 211.67 in 21CFR mandates that equipment and utensils be cleaned, maintained, and sanitized or sterilized at appropriate intervals to prevent malfunctions or contamination. The FDA emphasizes that contamination, which is reasonably avoidable and removable, is never acceptable. Cleaning procedures should be based on a scientific understanding of the substances and their interactions within the manufacturing facility.
The FDA accepts Total Organic Carbon (TOC) as an appropriate method for monitoring residues, provided the contaminating material is organic and contains oxidizable carbon. The FDA requires both rinse samples and direct surface measurements, such as swabbing, for effective residue monitoring and mandates a Continuous Verification Program for routine residue monitoring post-cleaning validation.
European Medicines Agency (EMA)
The EMA has established risk-based cleaning validation guidelines to prevent cross-contamination in shared production facilities. Effective from June 1, 2015, the EMA requires the establishment of Health-Based Exposure Limits (HBELs) for all drug products, with periodic reassessment of these limits throughout the product’s lifecycle. HBELs form the basis for additional controls through Quality Risk Management. Analytical testing at product changeover is required unless quantified risk is low, with risk assessed based on severity, probability, and detectability.
World Health Organization (WHO)
The WHO’s guidelines for cleaning validation align closely with those of the FDA, emphasizing the importance of continuous monitoring through analytical testing and visual examination. WHO supports the worst-case product approach for selecting representative APIs to validate cleaning procedures, considering factors like solubility and difficulty of cleaning, and calculates residue limits based on potency, toxicity, and stability.
ICH Guidelines
According to ICH Guidelines, for dedicated equipment, visual cleanliness is sufficient if supported by solid evidence from cleaning studies, including analytical tests. Regular cleaning is vital to prevent contamination buildup and maintaining API quality [ICH Q7, 5.23, 12.7, 12.76].Â
Acceptance criteria for residues should be established for both dedicated and non-dedicated equipment, with cleaning timing based on cleaning validation results to prevent contamination accumulation [ICH Q7, 5.22-25, 8.50].
During cleaning validation, visual inspection and analytical testing are essential to ensure effective cleaning. Subsequently, routine checks during product changeover should involve visual inspection, with analytical testing frequency determined by potential risks [ICH Q7, 12.72-76].
Pharmaceutical Inspection Co-operation Scheme (PIC/S)
The PIC/S guideline, effective from July 1, 2018, aligns with EMA’s risk-based cleaning validation approach, impacting over 50 member countries. The guideline includes an AIDE-MEMOIRE detailing specific regulatory expectations, making it an essential resource for pharmaceutical manufacturers.

Therapeutic Goods Administration (TGA)
The TGA has adopted the PIC/S Cleaning Validation Guideline, signalling a shift towards risk and science-based cleaning validation procedures. This adoption applies to medicines, active pharmaceutical ingredients, and biologicals containing live animal cells, tissues, or organs.
Health Canada
Health Canada’s Cleaning Validation Guidelines (Guide-0028) include unique requirements well-known in the industry but not widely mentioned elsewhere. The guidelines specify that the worst-case risk is acceptable along with the actual risk, though this approach is debated.
Parenteral Drug Association (PDA)
The PDA has published Technical Reports 29 and 49, which provide comprehensive guidance on cleaning validation for active pharmaceutical ingredients and biotechnology products. These reports align with lifecycle approaches to validation and ICH guidelines.
International Society for Pharmaceutical Engineering (ISPE)
The ISPE’s Baseline Guide on Risk-MaPP provides practical implementation details for establishing a cleaning validation SOP based on science and risk. It covers topics such as risk management, lifecycle approach, cleaning methodologies, and residue limits.
Active Pharmaceutical Ingredients Committee (APIC)
The APIC Cleaning Validation Guideline is widely used, especially in raw API material production. The 2016 revision incorporated EMA guidance on HBELs, with further updates in 2021 to address industry feedback and align better with EMA’s Q&A on HBELs.
American Society for Testing and Materials (ASTM)
ASTM’s Standard Guide for Science-Based and Risk-Based Cleaning Process Development and Validation incorporates concepts from FDA’s guidance for Industry Process Validation and ICH guidelines. Upcoming guides on visual inspection and cleaning validation limits are expected to become essential references for cleaning validation teams globally.
AmpleLogic Pharmaceutical Cleaning Validation Software
AmpleLogic’s Cleaning Validation Software is meticulously designed to comply with all major global regulations, including those set by the FDA, EMA, WHO, TGA, PDA, and APIC. This cutting-edge software offers a host of advanced features that streamline the entire pharmaceutical cleaning validation process. It generates template-based reports, provides real-time alerts, and ensures seamless authorization with timestamps, thereby enhancing traceability and accountability.
With its robust role-based access, the software guarantees secure handling of sensitive information while maintaining full visibility and transparency across operations. It assures quality and safety by effectively determining Maximum Allowable Carryover (MACO) limits, thus preventing contamination risks. Custom-built for the pharmaceutical industry, AmpleLogic’s software not only helps in maintaining compliance but also drives business process excellence through its highly customizable solutions, making it an indispensable tool for modern pharma companies.
The Cleaning Validation Journey
Designing the Cleaning Process
The foundation of successful cleaning validation in pharmaceutical industry begins with meticulous process design. AmpleLogic’s Cleaning Validation Software serves as the cornerstone, housing essential master data that encapsulates the intricacies of the cleaning process.
This includes vital information such as product manufacturing details, prescribed utensils, designated cleaning agents, and procedural guidelines mandated by regulatory authorities. Through this centralized repository, users can tailor cleaning protocols to adhere to specific regulatory standards, ensuring utmost precision and compliance.
Evaluating Cleaning Process Performance
Compliance with regulatory thresholds and guidelines is paramount in safeguarding product integrity and patient safety. AmpleLogic’s software facilitates rigorous evaluation of cleaning process performance, generating comprehensive reports aligned with regulatory stipulations. Leveraging advanced algorithms, it produces Worst Case Reports, calculates contamination limits, and furnishes efficiency analyses. Moreover, our system bolsters Maximum Allowable Carry Over (MACO) determinations for diverse product combinations, instilling confidence in regulatory adherence and process efficacy.
Continuous Monitoring for Process Optimization
In the dynamic landscape of pharmaceutical manufacturing, continuous monitoring is indispensable for upholding stringent quality standards. AmpleLogic pharma cleaning validation software’s innovative Process Scheduler feature empowers businesses to orchestrate cleaning procedures seamlessly, adhering to predefined schedules with precision. By harnessing master data inputs and conducting meticulous equipment inspections, the cleaning cycle unfolds methodically.
Real-time alerts promptly notify users of any deviations, enabling swift corrective action. Moreover, our system mandates detailed documentation of deviation reasons, enriching Efficiency Reports with actionable insights for process optimization and regulatory compliance.
Advantages of AmpleLogic Pharmaceutical Cleaning Validation Software
Streamlines Cleaning Validation in Pharma
AmpleLogic simplifies and accelerates the entire cleaning validation workflow, reducing manual labor and increasing efficiency. By automating processes, it saves time and resources, allowing teams to focus on critical tasks.
Generate Pharmaceutical Cleaning Validation Reports
The software effortlessly produces comprehensive cleaning validation reports using customizable templates tailored to your specific requirements. This feature ensures that documentation is thorough, consistent, and meets regulatory standards.
Template-based Regulatory Report Generation
AmpleLogic ensures consistency and accuracy in documentation by providing standardized templates for regulatory report generation. This feature simplifies compliance efforts and reduces the risk of errors in reporting.
Real-Time Alerts
The software enhances responsiveness by providing immediate notifications for critical deviations. This proactive approach allows teams to address issues promptly, minimizing the impact on operations and product quality.
Seamless Authorization with Timestamps
AmpleLogic maintains a robust audit trail with precise timestamps, ensuring traceability and compliance with regulatory requirements. This feature provides transparency and accountability in the validation process.
Visibility & Transparency
The software offers complete oversight of the cleaning validation process, promoting better decision-making and accountability. Stakeholders have access to real-time data, enabling informed decisions and proactive management of validation activities.
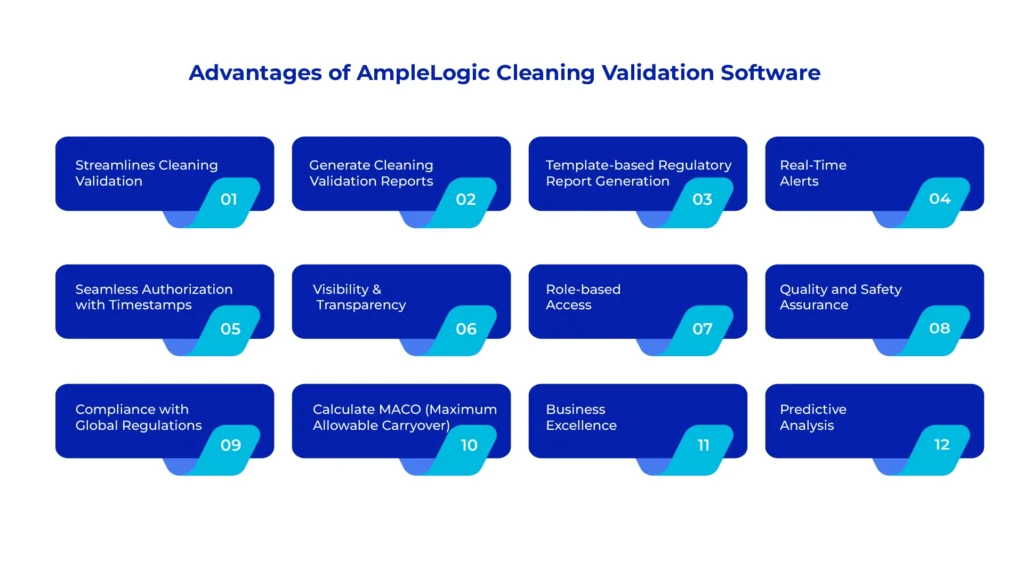
Role-based Access
AmpleLogic protects sensitive information with access controls tailored to different user roles, ensuring data security. This feature prevents unauthorized access and safeguards confidential information.
Quality and Safety Assurance
The software upholds high standards of product quality and patient safety by effectively managing contamination risks. By identifying and mitigating potential hazards, it helps ensure compliance with regulatory requirements and enhances patient trust.
Compliance with Global Regulations
AmpleLogic adheres to all major international regulations, ensuring your processes meet stringent industry standards. This feature minimizes the risk of non-compliance and helps organizations maintain a competitive edge in the global market.
Calculate MACO (Maximum Allowable Carryover)
The software determines Maximum Allowable Carryover (MACO) limits with precision, ensuring compliance with residue standards. This feature helps organizations avoid contamination issues and maintain product quality.
Business Excellence
AmpleLogic drives continuous improvement and operational efficiency, contributing to overall business success. By optimizing validation processes and promoting best practices, it helps organizations achieve their quality and performance objectives.
Predictive Analysis
The software employs advanced algorithms to foresee quality issues and compliance risks using historical data. This predictive analysis capability enables proactive risk management and enhances decision-making in validation activities.