Real-Time Monitoring: Implementing Dynamic Control Limits for Continuous Process Improvement in Pharma
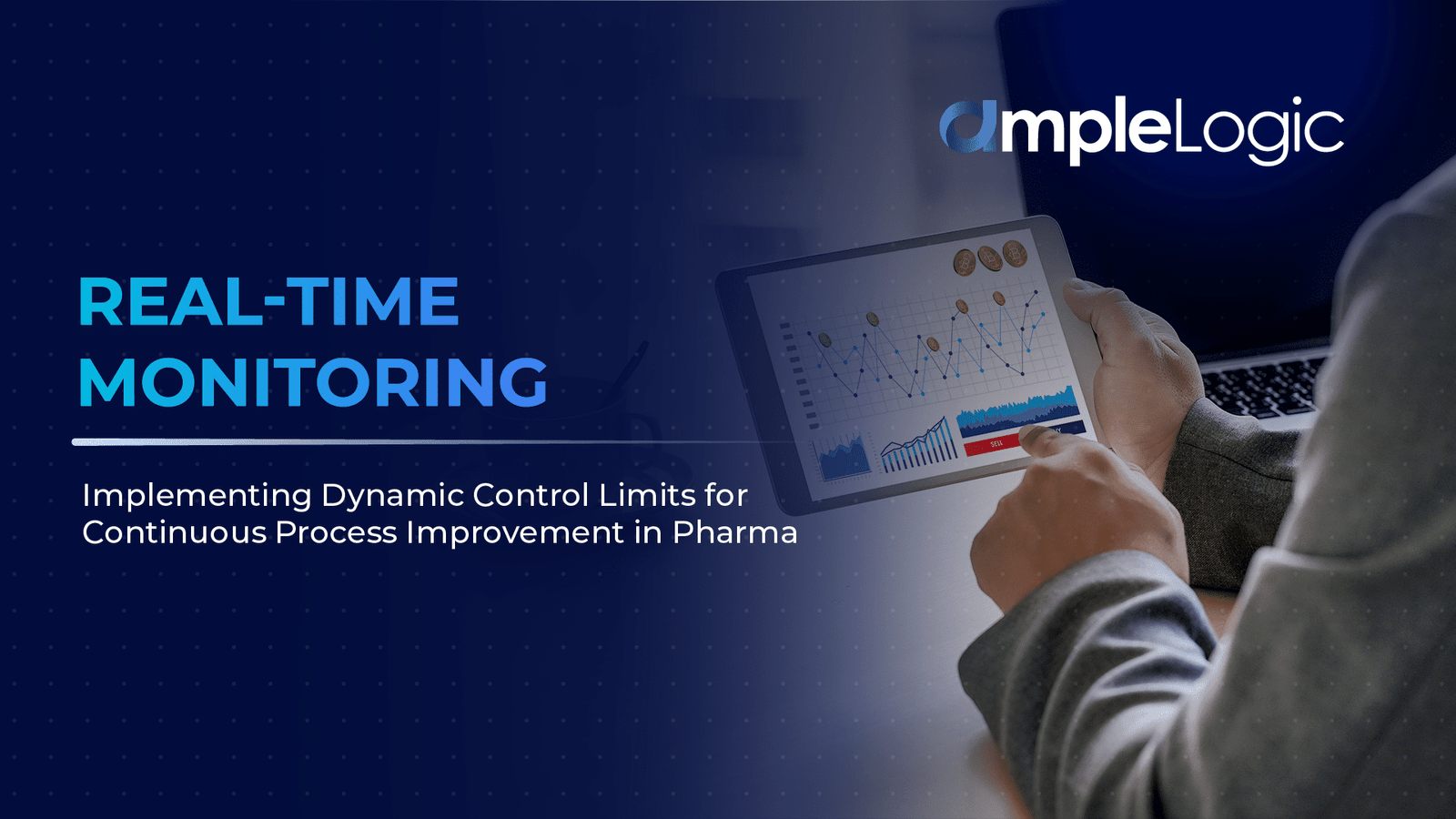
In pharmaceutical industry, ensuring quality and consistency of products is a top priority. Achieving this goal requires a commitment to continuous process improvement, a cornerstone of which is real-time monitoring. By leveraging real-time data analysis, pharmaceutical companies can swiftly detect deviations and fine-tune processes for optimal efficiency and quality. One effective strategy within this framework is the adoption of dynamic control limits, which facilitate proactive adjustments and elevate overall operational performance. This article delves into the significance of real-time monitoring and explores the transformative potential of dynamic control limits in pharmaceutical manufacturing.
Importance of Real-Time Monitoring in Pharma
Real-time monitoring entails the continual collection and analysis of data throughout the manufacturing process. This methodology offers a plethora of advantages within the pharmaceutical domain:
- Early Detection of Deviations: Real-time monitoring empowers manufacturers to swiftly identify deviations from established process parameters. This timely detection enables proactive interventions, preempting potential quality issues and safeguarding product integrity.
- Enhanced Process Understanding: Continuous monitoring provides invaluable insights into the intricate dynamics of the manufacturing process. By gaining a deeper understanding of variability, pharmaceutical companies can fine-tune critical parameters, thereby enhancing product quality and consistency.
- Compliance with Regulatory Standards: Regulatory agencies such as the FDA, EMA, MHRA, etc require pharmaceutical manufacturers to implement robust monitoring systems to ensure product quality and safety. Real-time monitoring helps companies comply with these standards by providing comprehensive data on process performance.
Dynamic Control Limits: Enhancing Process Control and Efficiency
Conventional control limits in manufacturing often rely on static thresholds derived from historical data. While effective to a certain extent, these static limits may falter in accommodating process variability and evolving conditions. In contrast, dynamic control limits offer a responsive and adaptive approach to process control, yielding several benefits for pharmaceutical manufacturing:
- Adaptability to Process Variability: Dynamic control limits support a culture of continuous improvement by promoting proactive problem-solving and process optimization. By addressing deviations promptly, pharmaceutical companies can drive ongoing enhancements in quality and efficiency.
- Early Warning Mechanism: By continuously analyzing process data, dynamic control limits serve as a proactive early warning system for potential issues. Any deviations from expected performance trigger immediate alerts, empowering operators to take preemptive actions and uphold process integrity.
- Cultivation of Continuous Improvement: Dynamic control limits foster a culture of continuous improvement by encouraging proactive problem-solving and process optimization. Promptly addressing deviations enables pharmaceutical companies to drive sustained enhancements in quality and operational efficiency.
Implementation Considerations
Successful implementation of dynamic control limits necessitates meticulous planning and seamless integration with existing systems. Key considerations include:
- Data Quality and Integration: Reliable data collection and integration are foundational to effective real-time monitoring. Pharmaceutical companies must ensure the accuracy, standardization, and seamless integration of data from diverse sources into the monitoring ecosystem.
- Analytical Capabilities: Advanced analytics tools are indispensable for processing large volumes of data and generating actionable insights in real-time. Companies may opt to invest in robust data analytics platforms or collaborate with technology partners to leverage cutting-edge analytical capabilities.
- Stakeholder Engagement: The successful deployment of dynamic control limits hinges upon collaborative engagement across various departments, including production, quality assurance, and engineering. Effective communication and stakeholder alignment are imperative to foster organizational buy-in and drive shared objectives.
Real-time monitoring and dynamic control limits emerge as indispensable enablers of continuous process improvement in pharmaceutical manufacturing. By harnessing the power of real-time data analytics and adaptive control strategies, companies can elevate product quality, optimize operational processes, and ensure compliance with regulatory mandates. As the pharmaceutical landscape continues to evolve, embracing innovative monitoring technologies will be pivotal in staying competitive and meeting the evolving needs of consumers and regulatory bodies alike.