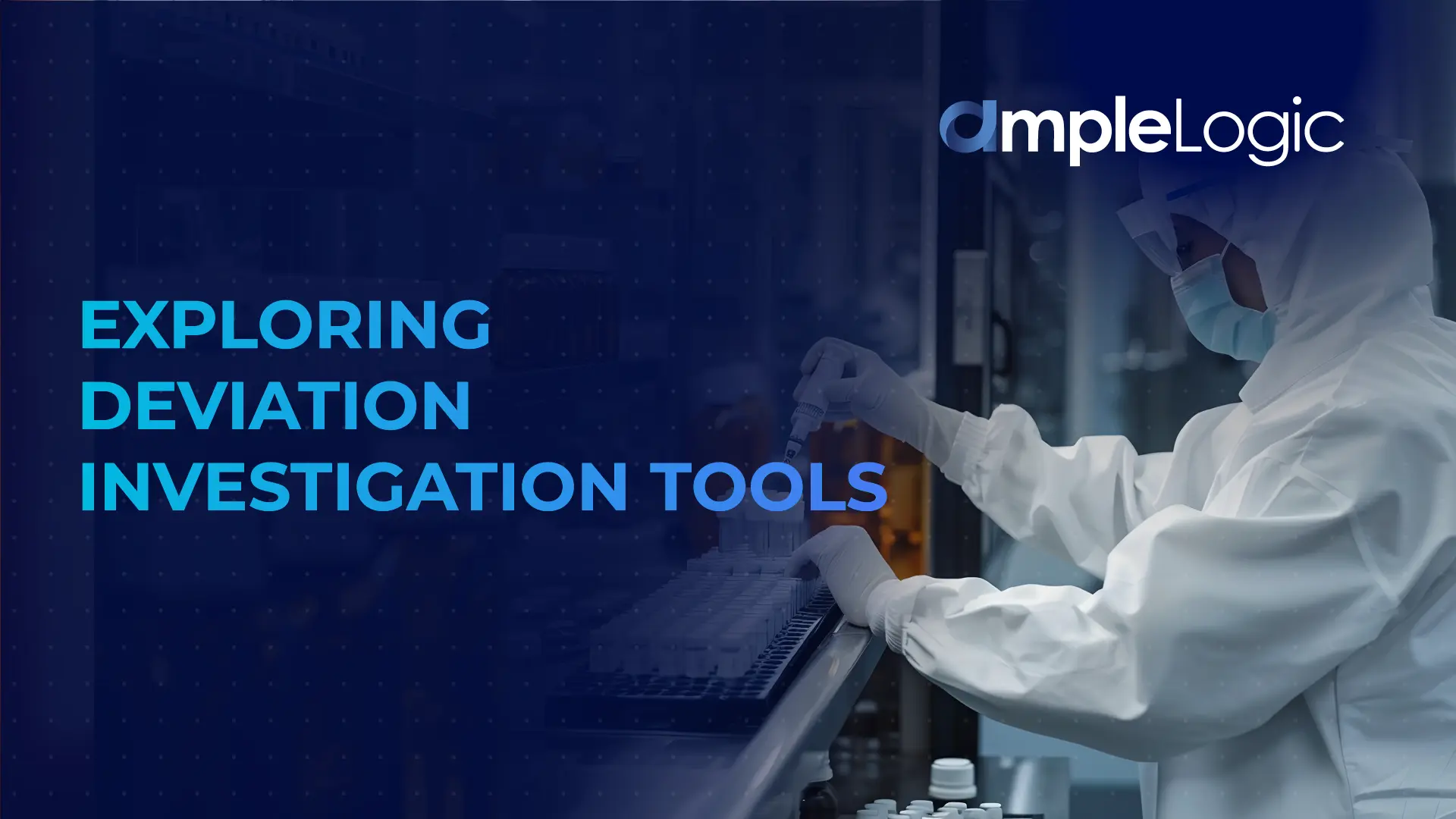
In the pursuit of operational excellence and quality assurance, deviations from established norms are not just expected but anticipated. However, what truly differentiates successful organizations is not the absence of deviations, but rather their adeptness in investigating and rectifying them promptly. Deviation investigation tools in pharma serve as the guiding compass in this journey, aiding organizations in unravelling the mysteries behind anomalies and ensuring continuous improvement.
Let’s embark on a journey to discover the diverse types of investigation tools in pharma and their indispensable roles in maintaining the integrity of processes and products.

Root Cause Analysis (RCA) Tools
At the heart of deviation investigation lies the quest to identify root causes. RCA tools, ranging from classic Ishikawa diagrams to sophisticated Fault Tree Analysis (FTA) software, empower organizations to delve deep into the underlying factors contributing to deviations. By systematically dissecting processes and scrutinizing contributing variables, RCA tools unveil the fundamental causes, paving the way for targeted corrective actions.
Fishbone Diagrams
Fishbone diagrams, also known as Ishikawa diagrams, offer a visually intuitive approach to root cause analysis. By categorizing potential causes into branches such as people, process, equipment, materials, and environment, fishbone diagrams facilitate brainstorming sessions and foster a holistic understanding of deviation triggers.

5 Whys Analysis
Rooted in the philosophy of iterative questioning, the 5 Whys technique is a simple yet powerful tool for uncovering root causes. By repeatedly asking “why” until reaching the underlying cause of a deviation, organizations peel away layers of complexity and reveal the core issues driving deviations.
Brainstorming
Brainstorming is a collaborative method where participants offer spontaneous ideas, fostering discussions to uncover the root cause of a deviation in a Quality Management System (QMS). By harnessing diverse perspectives, this approach ensures thorough consideration of all pertinent factors, aiding in the comprehensive understanding and verification of the deviation’s underlying cause.
Failure Mode and Effects Analysis (FMEA)
In high-risk industries such as aerospace, automotive, and healthcare, proactive risk mitigation is paramount. FMEA tools enable organizations to systematically evaluate potential failure modes, their effects, and the likelihood of occurrence. By prioritizing risks and implementing preventive measures, FMEA tools pre-emptively address deviations before they manifest into critical failures.
Statistical Analysis Software
In data-rich environments, deviations often leave digital footprints waiting to be deciphered. Statistical analysis software, ranging from industry standards like Minitab to open-source platforms like R and Python, equips organizations with the tools to crunch numbers, identify trends, and discern patterns indicative of deviations. From control charts to regression analysis, statistical tools empower organizations to transform raw data into actionable insights.
Cause-and-Effect (C&E) Matrix
As deviations unfold across interconnected processes, mapping the intricate web of cause-and-effect relationships becomes imperative. C&E matrices provide a structured framework for correlating potential causes with observed effects, guiding investigators in navigating the labyrinth of deviation pathways. By illuminating the causal linkages between variables, C&E matrices expedite the investigation process and inform targeted interventions.
Pareto Analysis
In the realm of deviations, not all causes are created equal. Pareto analysis, inspired by the Pareto principle, discerns the vital few from the trivial many by prioritizing root causes based on their frequency or impact. By focusing resources on addressing the most significant contributors to deviations, Pareto analysis enables organizations to achieve maximum leverage in their improvement efforts.
Incident Investigation Software
In today’s digitized landscape, manual deviation investigation processes are relics of the past. Incident investigation software streamlines and standardizes deviation investigations, from initial data collection to root cause analysis and corrective action tracking. With features such as configurable workflows, automated notifications, and centralized data repositories, incident investigation software enhances collaboration, transparency, and accountability across organizational silos.
Conclusion
By leveraging a variety of deviation investigation tools from traditional methods like root cause analysis and CAPA to advanced technological solutions pharmaceutical companies can thoroughly understand the causes of deviations and implement effective corrective actions. Embracing these tools equips organizations to navigate deviations with precision, ultimately strengthening their processes and enhancing overall resilience.