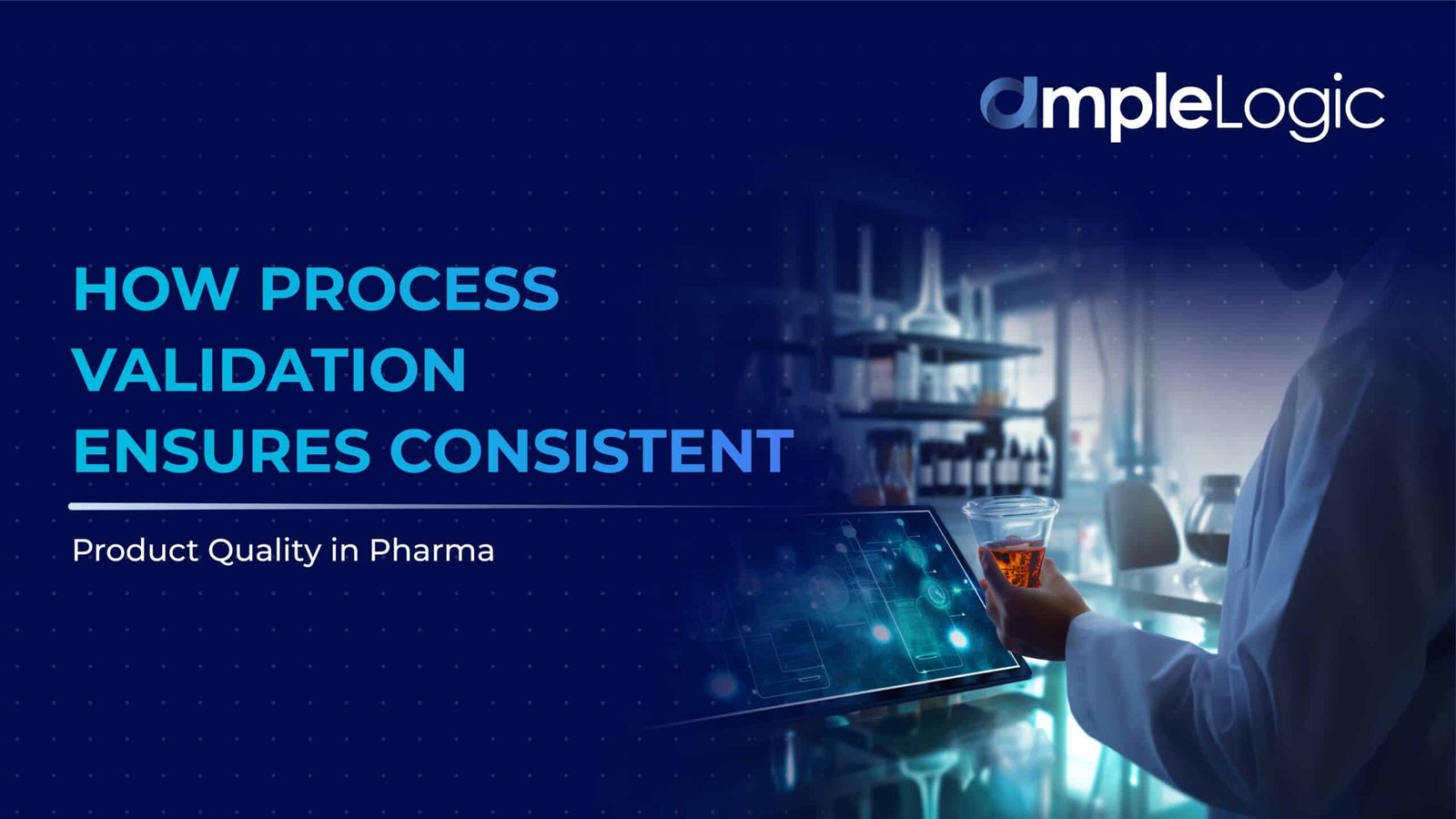
Ensuring superior product quality and safety is imperative in the pharmaceutical industry. Every process of pharma manufacturing is, hence, really important for guaranteeing production of desired products. In order to ensure that pharma products meet standardised quality, businesses need to implement effective process validation measures. Process validation is a key step in analysing the manufacturing processes and generating detailed reports for regulatory submissions. The evaluation is necessary for research and development (R&D), stability studies and for continuous monitoring of processes for maintain accuracy and product quality.
Understanding Process Validation
Process Validation is a reliable method by which pharma businesses can ensure standardised quality of their products. The validation method is implemented for registration batches as well as the manufacturing batches (upto 3 batches). In the pharmaceutical industry, it involves rigorous testing and documentation at every stage of the manufacturing process, from raw material handling to the final product. The goal is to identify and control variables that can affect product quality, ensuring that every batch produced is of the same high standard.
Stages of Process Validation
Process validation in pharmaceuticals is typically divided into three stages:
- Process Design: This initial phase involves developing the manufacturing process based on sound scientific principles. During this stage, Critical Process Parameters (CPP) and Critical Quality Attributes (CQA) are defined through research, experimentation and stability studies.
- Process Qualification: In this stage, the designed process is put into practice, and its performance is evaluated under actual production conditions. This involves validating the equipment, facilities, and processes to ensure they operate as intended. Process qualification confirms that the process, when executed according to the established parameters, will produce a product that meets all quality specifications.
- Continued Process Verification: After the process has been validated, it enters the phase of continued process verification. This ongoing stage involves continuous monitoring and evaluation of the manufacturing process during routine production to ensure it remains in a state of control. This is crucial for detecting any deviations that could affect product quality and for making necessary adjustments.
The Role of Process Validation in Ensuring Product Quality
- Consistency in Production: Process validation ensures that every batch produced meets the same quality standards. By rigorously controlling and monitoring the manufacturing process, pharmaceutical companies can minimize variability, leading to consistent product quality across all batches.
- Regulatory Compliance: Regulatory agencies like the FDA and EMA require pharmaceutical companies to conduct process validation to demonstrate that their manufacturing processes are capable of consistently producing quality products. Non-compliance can result in severe penalties, including product recalls or shutdowns. Process validation not only helps companies meet these regulatory requirements but also builds trust with regulators and consumers.
- Risk Mitigation: Through process validation, potential risks in the manufacturing process are identified and controlled before they can affect product quality. By proactively addressing these risks, companies can prevent costly errors, reduce waste, and avoid the need for rework or product recalls.
- Cost Efficiency: While process validation requires an initial investment in time and resources, it ultimately leads to cost savings. Consistent production processes reduce the likelihood of defects and waste, leading to more efficient use of materials and resources. In the long run, this efficiency translates to lower production costs and higher profitability.
- Improved Product Quality: Process validation focuses on understanding and controlling the factors that affect product quality. By ensuring that these factors are consistently managed, pharmaceutical companies can produce products that consistently meet or exceed quality standards, leading to better outcomes for patients and a stronger market reputation.
AmpleLogic Process Validation Software
AmpleLogic Process Validation Software is a standard solution for businesses to verify their processes continuously to attain superior quality products. By its implementation, businesses can monitor their processes and meet Critical Process Parameters and Critical Quality Attributes. AmpleLogic Process Validation Software generates template-based validation reports, auto-drafts protocols according to SOPs, integrates with other systems like ERP, QMS, APQR, etc, collects accurate data, analyses them and ensure continuous improvement. The solution offers effective change control, user-based access for security, risk assessment and management, integration with equipment like HPLC, balances, machines and much more!
By using the software, pharma businesses can ace quality assurance by systematically designing, qualifying and monitoring production processes. AmpleLogic Process Validation Software is completely customizable and comes with advanced features that guarantee consistent product quality, compliance with regulatory standards, and maintenance of consumer trust. As the industry evolves, the importance of robust process validation will only grow, making it an essential practice for any pharmaceutical company committed to excellence.