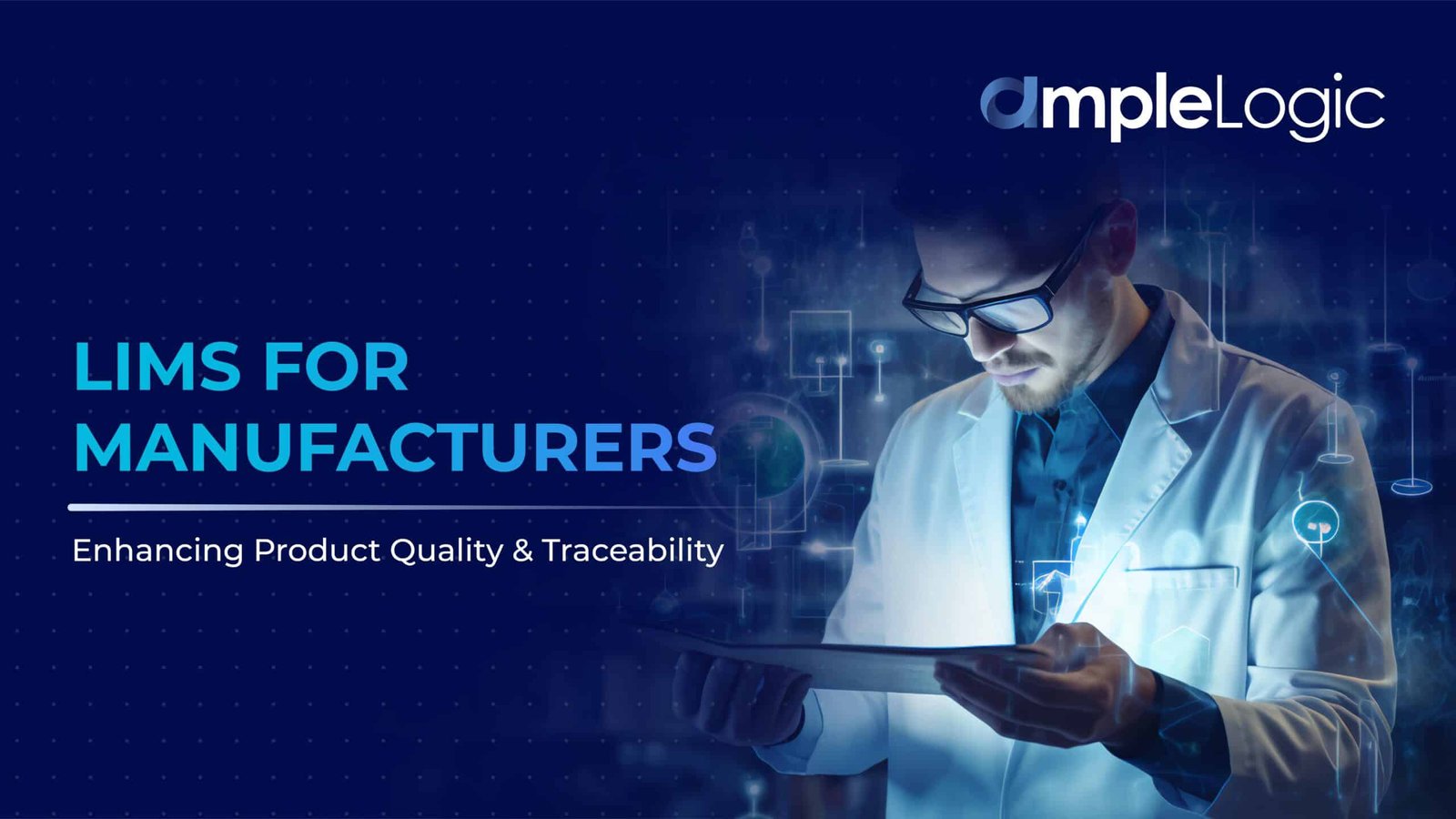
In today’s competitive pharmaceutical landscape, manufacturers need effective digital solutions that helps them maintain high product quality and product traceability in manufacturing for ensuring patient health and safety. In a pharma manufacturing facility, there are various departments and chronological processes or SOPs that are followed. Pharma Lab processes stand out as a major segment of pharma manufacturing. Right from researching on new pharma drugs to testing their quality, pharma labs, lab operators, technicians or research personnel play a critical role.
As we slowly adapt digitized pharma processes for accuracy and optimization of processes, pharma manufacturers are slowly adapting newer technical solutions for streamlining their lab operations for enhancing product quality and product traceability in manufacturing. LIMS is the biggest asset in this regard. Let’s navigate the topic a bit more.
Challenges in Pharma Lab Operations
Traceability Issues
- Lack of Raw Material Tracking: Inadequate tracking of raw materials from their suppliers to production facilities can create accountability gaps, complicate inventory management, and hinder effective recall management. When raw materials are not fully traceable, pinpointing the source of a defect or contamination becomes challenging, leading to delays and potential non-compliance.
- Incomplete Batch Records: Missing or fragmented batch records can disrupt audits, increase the risk of non-compliance, and complicate product traceability in manufacturing efforts. When data is incomplete or disorganized, tracking the quality and history of a batch becomes difficult, posing a significant risk to product safety and regulatory adherence.
- Complex Recall Processes: Inadequate or delayed identification of affected batches during product recalls can lead to prolonged resolution times, exposing the company to regulatory scrutiny and customer dissatisfaction. A slow or inefficient recall process can also put public health at risk, highlighting the importance of rapid action when issues arise.
- Poor Visibility Across Processes: Lack of centralized and real-time data visibility across different stages of the manufacturing process complicates the tracing of materials, products, and their associated quality data. Without comprehensive oversight, identifying issues and optimizing processes becomes significantly harder, leading to inefficiencies and increased risk of quality management in manufacturing.
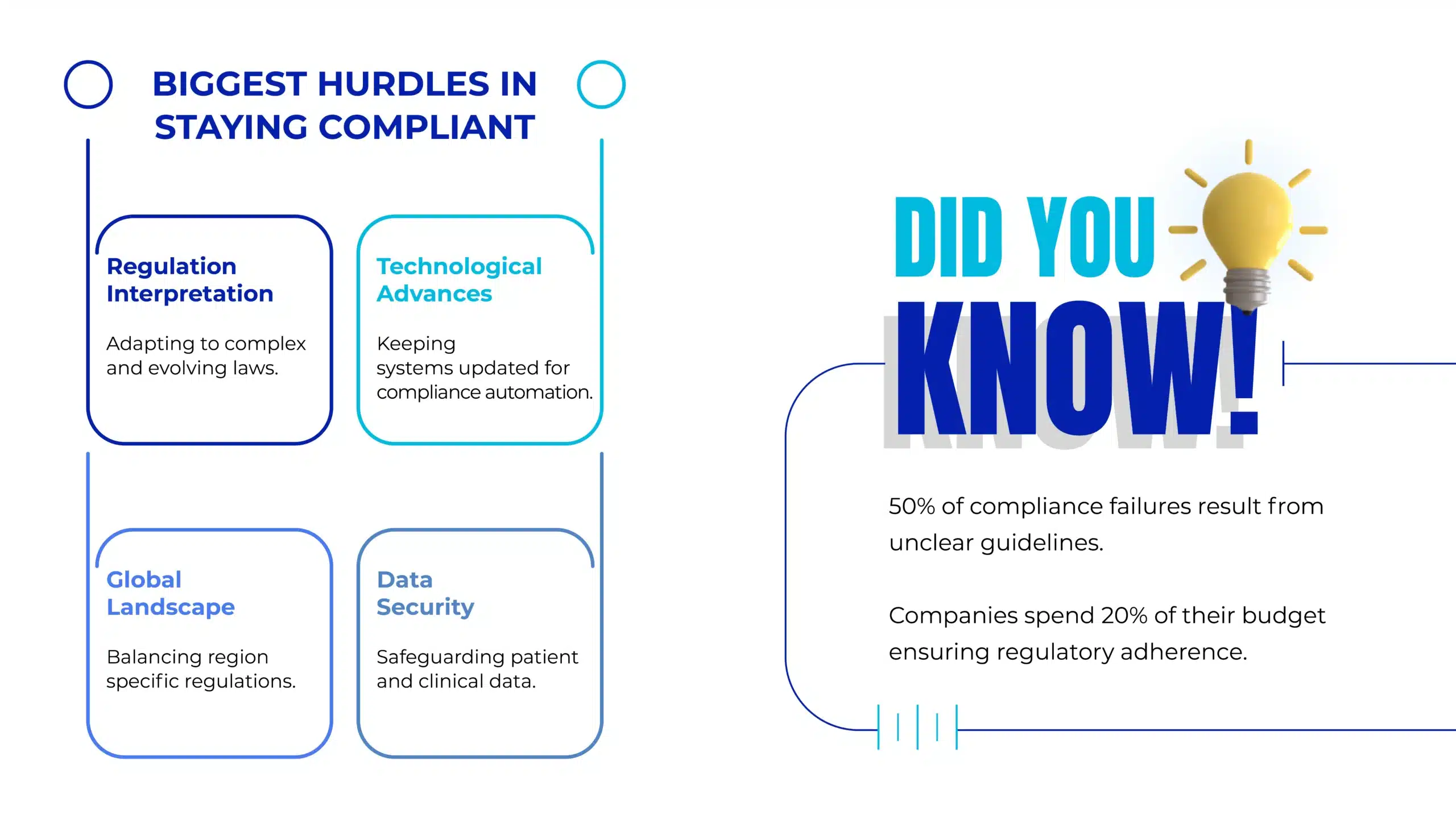
Quality Risk Adversities
- Inconsistency in Test Results: Variability in testing methods, equipment calibration, or human error can result in inconsistent or inaccurate test outcomes, ultimately compromising product quality and regulatory compliance.
- Data Integrity Issues: Manual errors, incomplete or falsified records, and inconsistent documentation can significantly compromise the integrity of critical test data, undermining compliance, product traceability in manufacturing, and product quality.
- Delayed Detection of Quality Issues: The inability to detect deviations or issues promptly during testing or production processes can result in substandard products, costly batch recalls, and significant safety hazards, damaging both reputation and bottom line.
- Non-Compliance with Regulations: Failing to comply with global regulatory standards such as GMP, FDA, ISO, or other industry requirements can lead to penalties, product recalls, legal action, and reputational damage.
Introducing LIMS Software for Pharma Manufacturers
Laboratory Information Management System (LIMS)Â is a critical tool for pharmaceutical manufacturers, designed to manage operations, data, and workflows with precision and efficiency. Acting as a central hub, LIMS streamlines manufacturing processes, enhances productivity, and ensures data integrity, all while supporting strict regulatory compliance. By handling large volumes of samples and automating routine tasks, LIMS helps pharmaceutical manufacturers improve quality management in manufacturing, optimize batch management, and meet industry standards seamlessly. Its role in maintaining compliance and ensuring product quality makes LIMS an indispensable solution for the pharmaceutical industry.
Benefits of LIMS
- Ensures Regulatory Compliance: Pharmaceutical manufacturing is governed by strict regulations like FDA (21 CFR Part 11), GMP, GLP, and ISO standards. LIMS for manufacturers ensure compliance by maintaining audit trails, enforcing ALCOA+ principles for data integrity, and generating reports for inspections, simplifying regulatory processes and reducing manufacturers’ burden.
- Improves Quality Control (QC): Quality is critical in pharmaceutical manufacturing, and LIMS enhances quality management in manufacturing by automating testing, managing schedules, and tracking results for raw materials and products. It enables real-time monitoring of deviations and OOS results, ensuring quick corrective actions. LIMS for production also standardizes protocols across batches, minimizing variability and ensuring consistent product quality.
- Streamlines Sample Management: LIMS simplifies handling large volumes of samples by automating tracking from receipt to disposal, ensuring accurate sample monitoring. It uses barcoding to prevent misidentification and tracks storage conditions like temperature and humidity to maintain sample integrity.
- Enhances Data Management and Integration: In pharmaceutical manufacturing, LIMS streamlines data management by centralizing test results, protocols, and reports in one system. It integrates with lab instruments to capture data directly, minimizing manual errors, and ensures role-based access so the right people can access the right information, improving accuracy and collaboration.
- Accelerates Research and Development (R&D): LIMS for manufacturers supports drug discovery and development by tracking experiments, ensuring reproducibility through recorded protocols, results, and modifications. It facilitates secure collaboration among teams and external partners, while enabling data mining to uncover insights from historical data, driving informed decision-making and accelerating drug development.
- Optimizes Batch Release: In batch production, LIMS ensures efficiency and compliance by tracking batch status and QC tests in real-time, verifying that quality parameters are met before release, and automating the generation of Certificates of Analysis (CoAs) for finished products, simplifying documentation and ensuring accurate quality management in manufacturing.
- Reduces Costs and Increases Efficiency: LIMS for production automates and centralizes workflows, reducing manual effort and eliminating repetitive tasks like data entry and sample tracking. This increases efficiency, minimizes errors, and accelerates turnaround times by providing real-time data access, improving decision-making and overall productivity in pharmaceutical manufacturing.
- Supports Continuous Improvement: Pharmaceutical manufacturers can use LIMS data to identify trends, address inefficiencies, and optimize processes through data-driven insights. It helps improve performance and scalability by integrating with systems like ERP and MES, ensuring smooth expansion and consistent data flow across production stages.
LIMS Enhancing Pharma Product Quality
LIMS for manufacturers automates and standardizes testing workflows, integrating directly with lab instruments to ensure consistent, precise, and repeatable results across all quality tests, reducing human intervention and minimizing manual errors to enhance test accuracy and streamline operations. It enforces robust data integrity controls, including audit trails, version control, and role-based access permissions, ensuring that all data remains accurate, secure, and tamper-proof while adhering to regulatory standards such as FDA 21 CFR Part 11. Additionally, LIMS for manufacturers provides real-time monitoring of test data and production processes, instantly flagging deviations and out-of-spec results, sending immediate alerts for corrective actions to proactively address issues before they escalate, minimizing risks of defective products, non-compliance, and costly recalls.
Furthermore, LIMS for production automates regulatory compliance by generating essential documentation such as Certificates of Analysis (CoA) and batch records, ensuring adherence to predefined quality standards, streamlining regulatory reporting, and reducing the risk of audits, fines, or regulatory action, offering full assurance that testing and production processes meet necessary compliance requirements.
Boosting Traceability with LIMS
A Laboratory Information Management System (LIMS) ensures precise tracking of raw materials by lot numbers, seamlessly integrates with supply chain systems, and provides full traceability from the supplier to production, enhancing accountability, recall management, and transparency across the manufacturing process. It centralizes and links all testing results, raw materials, and process data directly to Batch Manufacturing Records (BMR), ensuring complete, accessible, and compliant batch records that facilitate smooth audits and improve traceability. LIMS for production also provides end-to-end product traceability in manufacturing, enabling quick identification of affected batches and their distribution channels, streamlining recall management, and ensuring swift corrective actions for effective quality management in manufacturing. By consolidating data from raw materials to finished goods into a single platform, LIMS for production improves decision-making, optimizes resource allocation, and proactively manages quality issues, ultimately enhancing production efficiency and compliance.
With an effective LIMS solution, pharmaceutical manufacturers can produce excellent pharma products with improved quality and traceability. With automation of key processes, efficient data management, and real-time traceability of pharma products from testing of raw materials to the finished products, Laboratory Information Management System ensures no area is lying under the rock. With LIMS, pharma manufacturers can minimize risks, implement advanced quality control, optimize batch release, and accelerate research, making the solution an invaluable tool for meeting industry standards and maintaining superior product safety and competitiveness.