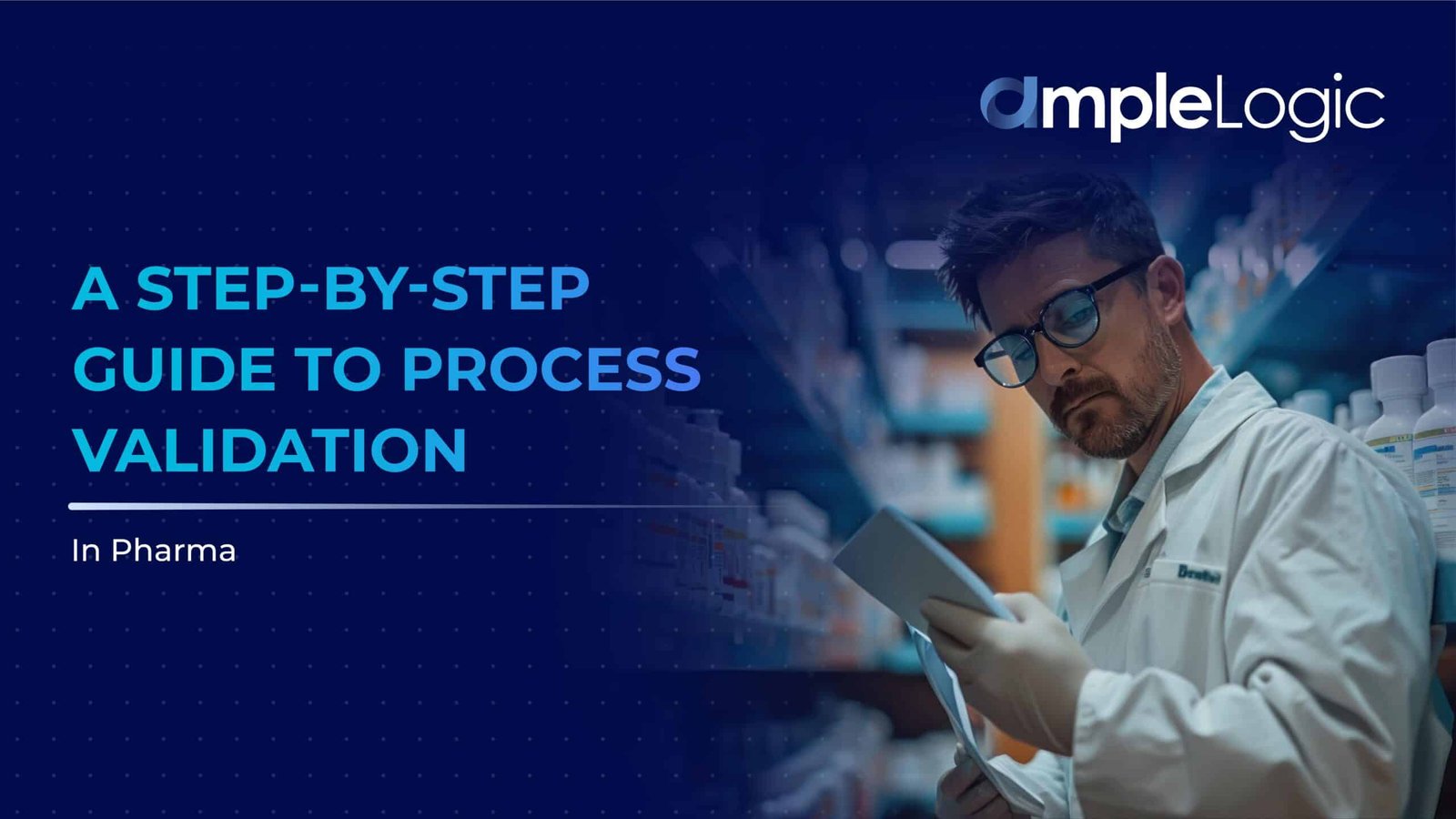
Process Validation is a critical step in the pharma industry to ensure enhanced product quality and regulatory compliance. The process validation process involves extensive documentation of processes, their proper evaluation and finally, report generation for regulatory submissions. The method of process validation in pharma is quite lengthy and requires assistance of various systems and integration with equipment. It is important that companies take a step-by-step approach for process validation in pharma. This guide provides an overview of the process validation in pharma, highlighting key stages, regulatory requirements, and best practices.
Understanding Process Validation
Process Validation encompasses the evaluation of processes by defining Critical Process Parameters (CPP) and Critical Quality Attributes (CQA) to understand if processes meet these criteria and consistently deliver high quality products. With an effective process validation method in place, pharma companies can ensure their products meet the predetermined quality attributes, identification and control of variables that affect product quality and support regulatory compliance, reducing risks of product recalls or non-compliance issues.
Three Stages of Process Validation
Stage 1: Process Design
The first stage of process validation is process design wherein pharma manufacturing processes are first defined including critical parameters such as CPP and CQA. This includes capturing integral data from testing of registration batches and their stability studies.
Key Activities include:
- Conduct risk assessment to identify potential critical quality attributes (CQAs) and critical process parameters (CPPs)
- Develop a process control strategy
- Pilot-scale studies to fine-tune the process
- Use Quality by Design (QbD) principles to enhance understanding and control
Stage 2: Process Qualification
In this stage of process validation, the process design is evaluated to understand that it can consistently deliver high-end pharma products throughout commercial manufacturing cycle.
Key Activities include:
- Installation Qualification (IQ): Verify that equipment and utilities are installed correctly and operate as intended
- Operational Qualification (OQ): Test the operation of the equipment and systems under the worst-case conditions
- Performance Qualification (PQ): Validate the entire production process with real product and under commercial manufacturing conditions
- Conducting three consecutive batches to demonstrate process consistency
Stage 3: Continued Process Verification (CPV)
The third stage of process validation involves continuous monitoring and evaluation of commercial pharma manufacturing processes to ensure that that CPPs and CQAs are met. At this stage it is ensured that processes remain in a state of control during commercial pharma production.
Key Activities include:
- Continuous monitoring of process parameters and quality attributes
- Implementation of a robust deviation management system
- Periodic review of process data and requalification as necessary
- Ensuring timely updates to the control strategy based on data trends or changes in the manufacturing process
Key Considerations and Best Practices
Risk Management
Implementing risk management principles (ICH Q9) throughout the process validation lifecycle and prioritizing high-risk areas for enhanced control and monitoring.
Documentation
Maintaining thorough documentation for each validation stage in the form of protocols, reports, and records of all activities. Also, ensuring traceability of data and decisions to support audits and inspections.
Training and Competency
Providing ongoing training for personnel involved in process validation and developing a competency matrix to ensure that all team members are qualified to perform their roles.
Cross-Functional Collaboration
Encouraging collaboration between R&D, quality assurance, manufacturing, and regulatory teams. Involving all stakeholders in the validation planning and execution to ensure alignment and understanding.
Regulatory Submission
Compiling a comprehensive validation package for regulatory submissions and addressing specific requirements outlined by regulatory agencies such as FDA, EMA, etc.
Introducing AmpleLogic Process Validation Software
As process validation in pharma is an elaborate task, it is mandatory that businesses implement advanced solutions that takes care of the pharma validation process, ensuring efficiency and accuracy. With AmpleLogic Process Validation Software, pharma companies can easily streamline their process validation operation with unique integration capabilities. The application is tailor-made for the pharma industry and helps businesses produce exceptional quality products with accurate data collection and analysis. AmpleLogic’s solution offers auto-protocol drafting according to the company’s SOPs, advanced verification with electronic signatures, real-time monitoring of all processes, risk assessment and management, assists in continued process validation in pharma and generates template-based process validation reports instantly!
Now delve into the future of process validation in pharma! AmpleLogic Process Validation software enables pharma companies to adhere to a structured approach for process validation. It enhances manufacturing efficiency while enabling regulatory compliance and quality assurance. Effective process validation is not just a regulatory requirement but a cornerstone of patient safety and product reliability. With AmpleLogic Process Validation transform your validation process today!