Implementing ALCOA+ in Your Manufacturing Processes

In the pharmaceutical industry, the integrity of data is paramount. Originally, the ALCOA principles—Attributable, Legible, Contemporaneous, Original, and Accurate—were established to ensure data integrity in regulated industries. These principles have since evolved to include four additional criteria: Complete, Consistent, Enduring, and Available, forming the ALCOA+ framework. This expanded set of guidelines provides a more comprehensive approach to data management, particularly in manufacturing processes within the life sciences sector.
The Genesis of ALCOA Principles
The ALCOA principles were developed in response to the growing complexity of data management in the pharmaceutical industry. As technology advanced, so did the need for a standardized approach to ensure data reliability and authenticity. ALCOA, which stands for Attributable, Legible, Contemporaneous, Original, and Accurate, was introduced to address these needs comprehensively. This framework helps ensure that all data recorded in the pharmaceutical industry can be trusted, from initial research and development through to manufacturing and quality control.
Deep Dive into ALCOA+ Principles
Attributable
The principle of being Attributable focuses on the ability to trace data back to its origin. This means every piece of data must be linked to the person who generated it. In the pharmaceutical industry, this is crucial for accountability and traceability. Methods to ensure attribution include electronic signatures, detailed log entries, and secure user authentication systems. This helps in identifying the source of data and understanding the context in which it was generated, which is vital during audits and inspections.
Legible
Legibility is about ensuring that data is clear, readable, and understandable. In the context of pharmaceutical records, this means maintaining documentation that can be easily interpreted by anyone reviewing it, including regulators and auditors. Poorly written or ambiguous data can lead to misinterpretations, errors in decision-making, and potential regulatory non-compliance. To uphold legibility, companies must implement standardized documentation practices and use digital tools that support clear and consistent data entry.
Contemporaneous
Contemporaneous data recording means documenting data in real-time as events occur. This principle is essential for maintaining an accurate and reliable timeline of activities and decisions. Recording data contemporaneously ensures that information is captured accurately, reflecting the true sequence of events. This practice supports compliance, operational efficiency, and enhances the credibility of the data, as it reduces the risk of retrospective alterations and errors.
Original
The principle of Originality emphasizes the importance of maintaining original records and preventing alterations. Original data serves as the primary source of truth and should be preserved in its initial form. The use of electronic systems with robust audit trails helps ensure that data remains unaltered, and any modifications are documented with appropriate justification. This enhances the reliability of the data and supports regulatory compliance.
Accurate
Accuracy in data recording means ensuring that the data is error-free and precisely reflects the observed findings. Accurate data is essential for making informed decisions and maintaining the quality and safety of pharmaceutical products. Strategies to enhance accuracy include rigorous training for staff, automated data capture systems, and regular audits and reviews to identify and correct errors promptly.
The Evolution to ALCOA+ Principles
The ALCOA principles have been expanded to ALCOA+ to address the growing complexities of data management in modern manufacturing processes. The additional principles include:
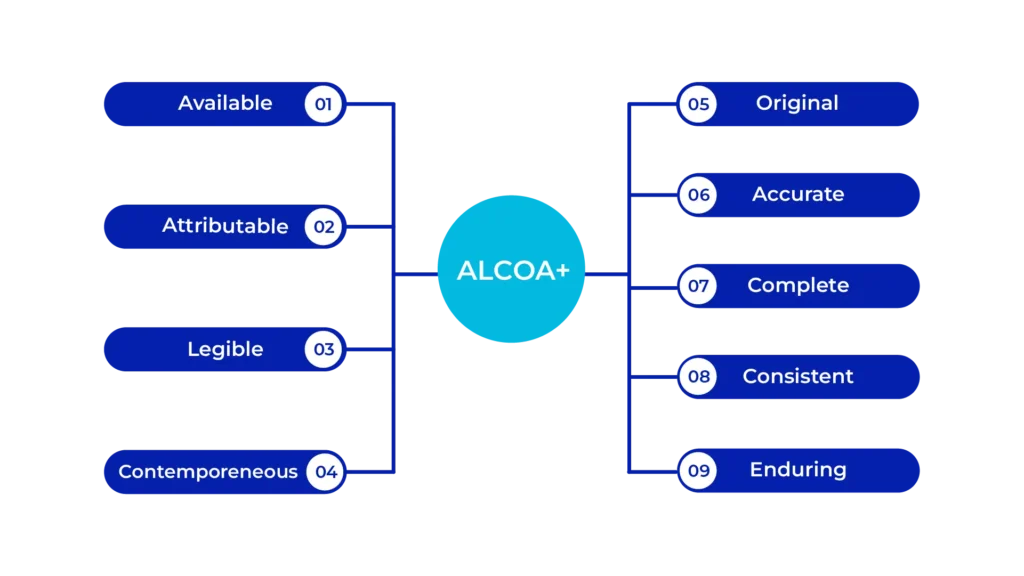
Complete
Data must be comprehensive, including all relevant information, metadata, and context. This ensures that no critical details are omitted, which could affect the interpretation or outcome of data analysis.
Consistent
Data must be recorded in a uniform manner across different systems and processes. Consistency in data formatting and documentation helps in maintaining integrity and reliability.
Enduring
Data must be maintained and accessible over the entire required retention period. This ensures that data is preserved for future reference, audits, and compliance checks.
Available
Data should be readily accessible to authorized personnel when needed. This facilitates timely decision-making and ensures compliance with regulatory requirements.
Integrating ALCOA+ into Manufacturing Processes
For life science manufacturers, integrating ALCOA+ principles into their data management systems involves a strategic approach. Here are key steps to effectively incorporate these principles:
1. System Design and Architecture
Design data management systems with built-in capabilities to capture and record data in alignment with ALCOA+ principles. This includes implementing audit trails, secure access controls, and robust data storage solutions to ensure data is attributable, legible, and enduring.
2. Standard Operating Procedures (SOPs)
Develop and enforce SOPs that reflect ALCOA+ principles. These procedures should outline how data is collected, recorded, verified, and stored. Regular training and updates for staff ensure that everyone understands and adheres to these standards. AmpleLogic’s Document Management System (DMS) adheres to ALCOA+ principles, enabling users to create, update, manage and access their SOPs and documents whenever it’s convenient for them.
3. Technology and Automation
Leverage technology and automation to enhance data integrity. Automated data capture systems reduce human error and ensure contemporaneous and accurate data recording. Integration of electronic batch records (EBR) and Laboratory Information Management Systems (LIMS) can support the consistent and complete documentation of data.
4. Regular Audits and Reviews
Conduct regular audits and reviews of data management practices to ensure compliance with ALCOA+ principles. This includes verifying data accuracy, completeness, and accessibility. Audits help identify gaps or areas for improvement and ensure continuous adherence to best practices.
5. Training and Culture
Foster a culture of data integrity within the organization. Regular training sessions on ALCOA+ principles and the importance of data integrity help embed these values in daily operations. Encouraging open communication and reporting of data issues helps in continuously improving data management practices. Our Learning Management Software integrates ALCOA+ principles which will help any manufacturer who might be looking to enhance the productivity and quality of work in their manufacturing processes.
Conclusion
The evolution from ALCOA to ALCOA+ reflects the increasing complexity and regulatory demands in the life sciences sector. By integrating these expanded principles into their manufacturing processes, life science manufacturers can enhance data integrity, ensure compliance, and improve overall operational efficiency. Implementing ALCOA+ is not just about meeting regulatory requirements but also about fostering a culture of excellence and reliability in data management.